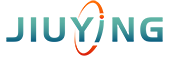
What Are You Looking For?
Transformer bushings are insulating devices that connect the transformer windings to external circuits. They provide electrical insulation between the windings and the transformer tank while mechanically securing the leads. During operation, bushings continuously carry load current and must withstand short-circuit currents during faults. Key requirements include:
(1)Adequate electrical and mechanical strength.
(2)Thermal stability to handle short-circuit overheating.
(3)Compact design, lightweight, strong sealing, versatility, and ease of maintenance.
Components: Terminal block, lead connector, rain shield, oil gauge, oil plug, oil conservator, upper porcelain insulator, end screen, lifting ring, oil sampling valve, nameplate, vent plug, connecting sleeve, lower porcelain insulator, and grading ring.
1.Insulation System: A multi-layer cylindrical capacitor core made of oil-impregnated cable paper and aluminum foil grading electrodes serves as the primary insulation. The porcelain shell acts as external insulation and houses the transformer oil.
2.Sealed Design: The internal oil system is isolated from external environments.
3.Mechanical Assembly: Heavy-duty springs compensate for thermal expansion and ensure sealing.
Oil Conservator: Adjusts oil volume changes due to temperature, preventing excessive pressure.
Grading Ring (Tail): Optimizes electric field distribution, reducing insulation gaps between the bushing and grounded components.
End Screen: Used for dielectric loss testing and partial discharge tests. It must remain grounded during normal operation.
Viewed from the high-voltage side:
High Voltage: O, A, B, C (left to right).
Medium Voltage: Om, Am, Bm, Cm.
Low Voltage: O, a, b, c.
1.Single Insulation: Porcelain or resin.
2.Composite Insulation: Oil-filled, epoxy-filled, or gas-filled.
3.Capacitor-Type: Oil-paper or resin-impregnated paper.
Oil-Paper Capacitor Bushings: Further divided into "cable-through" and "direct-conductor" types based on current-carrying structures.
The core consists of a hollow copper conductor wrapped with 0.08–0.12 mm cable paper and alternating 0.01/0.007 mm aluminum foil layers. This creates a graded voltage distribution, minimizing size and weight while ensuring uniform electric field strength.
1.Sealing Issues: Poor sealing at the top may cause water ingress and insulation failure; bottom leaks lead to oil loss.
2.Contamination: Dirty or moist surfaces increase leakage currents, causing flashovers, cracks, or insulation breakdown.
3.Testing & Repair:
Inspect porcelain for cracks, check oil levels, and ensure end-screen grounding.
Perform dielectric loss and insulation tests. Replace defective components.
Verify bushing type, electrical test results, and oil quality.
Ensure proper alignment, avoid twisting leads, and secure terminal connections.
Use apropriate lifting techniques to prevent porcelain damage.
The capacitor core must be vacuum-impregnated to eliminate air gaps and prevent partial discharge.
Tapered core ends ensure equal voltage distribution across grading layers.