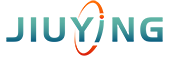
What Are You Looking For?
As global grid standards rise in complexity and rigor, utilities and equipment manufacturers face increasing pressure to ensure that cable withstand testing can be executed without disassembly. Across markets such as Belgium and utilities like Saudi Electricity Company (SEC) and Tenaga Nasional Berhad (TNB), it is now a common requirement that high-voltage withstand (HiPot) testing be conducted directly from the Ring Main Unit (RMU) — with the cable left in place.
The IEC62271-200 standard offers explicit guidance for this functionality. It stipulates that switchgear and controlgear may be designed to permit cable testing while still connected to the equipment. This can be achieved via designated test connectors or specialized cable terminations. The equipment must be capable of withstanding rated cable test voltages applied to parts still energized and connected during the test. At the same time, the test voltage must be effectively imposed on the corresponding cable segments.
The standard requires a dual-mode voltage application:
Phase-to-Ground on Busbar Side: A single-phase voltage equal to the rated system voltage (Ur) is applied between the busbar side (with all poles interconnected) and ground.
Cable Core Voltage Application: Each cable phase, one at a time, is subjected to the rated cable test voltage (Uct) — whether AC or DC — while all non-test phases are grounded.
Both voltage applications must occur concurrently. Markets governed by IEC frameworks often mandate the provision of fixed withstand test terminals within the RMU itself.
For example, the SEC Distribution Materials Specification requires an independent testing bushing — clearly stating that disconnecting the cable or applying test devices directly on the bushing is not acceptable.
This requirement has gained traction across IEC-centric markets. Leading OEMs have already incorporated design accommodations:
Schneider RM6: Equipped with removable earth bars, this unit allows high-voltage testing of cables connected at the bushing without disconnecting them from the system.
ABB SafeRing: Incorporates dedicated bushings specifically designed as withstand test terminals, enabling safe, efficient test access.
The concept is elegantly simple yet technically robust. In typical three-position earthing switch configurations, removing the static contact’s shorting bar and installing an insulated support frame allows for the test terminals to interface with all three phases. Each earthing contact is then extended via copper busbars to individual high-voltage test bushings. During normal operation, a shorting bar grounds the bushings. For testing, the bar is removed, and a test probe is mounted on the bushings to carry out withstand voltage verification.
This configuration is widely accepted for its safety, reliability, and operational clarity.
In cabinets using load break switch (LBS) configurations — commonly referred to as “C cabinets” — generous internal space allows for optimized busbar routing. This ensures adequate electrical clearance between test terminals, incoming phase bars, and the grounded enclosure.
In SF₆-insulated RMUs, insulation requirements are typically met with a clearance of over 40 mm at 17.5 kV. This provides ample margin to maintain dielectric integrity while routing copper bars for test access.
Advanced RMU designs incorporate knife-blade-style grounding doors, which offer intelligent mechanical interlock. Closing the test bushing compartment door automatically grounds the terminals, while opening the door exposes the bushings for testing. This dramatically reduces manual intervention — no tools, no bar removal — enhancing field efficiency and minimizing human error.
However, due to elevated costs and design complexity, such features remain relatively rare in widespread deployments.
In eco-friendly gas-insulated RMUs (using alternatives to SF₆), new design challenges emerge. Copper bus routing becomes particularly intricate due to spatial constraints and the need to maintain larger electrical clearances. For example, at 24 kV, a minimum separation of 150 mm may be required under low-pressure gas conditions.
Further complications arise when withstand testing is mandated for circuit breaker panels, not just LBS modules. These panels often lack the physical real estate to accommodate dual-mechanism switchgear (three-position isolator plus vacuum breaker) alongside heavy-duty copper test busbars. Given the busbars must tolerate short-duration fault currents, sufficient cross-sectional area is non-negotiable — demanding precision-engineered layouts.
Though technically feasible, these enhanced solutions inevitably increase engineering complexity. Manufacturers must weigh the cost-benefit ratio — balancing the necessity of in-place cable testing with design economy and field reliability.
Safety remains paramount. Any solution must guarantee operator protection, maintain system integrity during and after testing, and allow fast restoration of the original grounding state. Especially in eco-gas RMUs, where dielectric margins are tighter, maintaining sufficient creepage and clearance becomes a critical engineering task.
The goal is clear: enable rapid, secure, and maintenance-free withstand testing — without sacrificing continuous, reliable earthing or overburdening the system with unnecessary complexity. Only through meticulous optimization and a deep understanding of switchgear architecture can a truly future-proof solution be achieved.