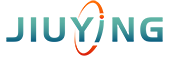
What Are You Looking For?
The outer shell of a dry-type transformer is its first line of defense. Any deformation, denting, or fissuring—often caused by mechanical impact or prolonged corrosion—can compromise both structural integrity and ingress protection. Even minor damage could escalate into significant performance degradation or safety hazards.
Grounding must also be meticulously examined. The grounding terminal should be firmly secured, free from oxidation or physical wear. Ground wires must be intact, with no visible corrosion or disconnection. The grounding resistance should comply with industry benchmarks, typically under 4 ohms, to ensure fault currents are safely discharged into the earth.
The windings, typically encased in high-grade insulating materials, must show no signs of conductor exposure. Bare wires can lead to catastrophic short circuits or ground faults.
All insulating elements—bushings, cylinders, and spacers—require close scrutiny. Their surfaces should be smooth, clean, and devoid of particulate contamination. Accumulated dust or chemical residues can act as conductors, reducing dielectric strength. Furthermore, cracks or structural defects in any insulating part can severely diminish electrical endurance, inviting partial discharge or arc faults.
A healthy dry-type transformer emits a consistent, low-frequency hum. Abrupt increases in volume, irregular buzzing, or foreign acoustic signatures may be symptomatic of overloading, magnetic core loosening, or inter-turn faults.
A distinct "sizzling" or "crackling" sound can signal partial discharges—often a precursor to insulation breakdown or coil deterioration. Timely diagnosis through sound can preempt severe electrical incidents.
Temperature regulation is central to transformer longevity. Most dry-type transformers are fitted with thermometric instruments such as resistance temperature detectors (RTDs) or capillary-type gauges. These indicators must register within prescribed thermal limits.
For F-class insulation, average winding temperature rises should not exceed 100K above ambient (typically 40°C). H-class systems can tolerate peak temperatures up to 155°C, though continuous operation near this threshold is ill-advised.
Air-forced cooling systems, including axial fans, must operate efficiently. Malfunctions—be they mechanical failures, reverse spinning, or abnormal fan noise—can precipitate thermal runaways.
Real-time tracking of current and voltage on both primary and secondary terminals is imperative. The transformer must not exceed its rated current. A triphasic imbalance may hint at phase loading discrepancies or internal asymmetry.
Voltage variation should remain within ±5% of nominal values. Deviations beyond this range can impair performance and shorten the lifespan of both the transformer and its downstream equipment.
Transformers require effective convective airflow to expel internally generated heat. The installation site must support unimpeded ventilation. Air inlets and exhausts should be free of obstructions; ducts must be intact and fans or HVAC units must run without anomalies.
Thermal stagnation due to inadequate airflow can reduce transformer efficiency and raise the risk of overheating-induced failure.
Environmental factors play a pivotal role in transformer reliability. Excessive ambient heat intensifies internal losses, while high humidity can degrade insulation resistance and promote surface tracking.
An optimal environment maintains temperatures below 40°C and relative humidity under 85%. Installing a thermo-hygrometer ensures continual monitoring, helping prevent adverse atmospheric effects.
Rodents and insects pose hidden dangers. Rodents may chew through insulation or wiring, initiating faults. Insects can nest within enclosures, introducing debris or conductive contaminants.
The transformer vicinity should be inspected for burrows, gnaw marks, or insect colonies. Preventive actions—such as sealing entry points and maintaining cleanliness—are essential to uphold long-term system integrity.
Routine and meticulous inspection of dry-type transformers is essential to ensure performance, longevity, and safety. From structural integrity to thermal management and environmental conditions, each element plays a critical role. By implementing a comprehensive inspection regimen, potential failures can be anticipated and mitigated—safeguarding both assets and operational continuity.