Transformer bushings are critical components that serve as current-carrying elements, connecting the internal high- and low-voltage leads of a transformer to the external tank. They provide mechanical support for the leads and ensure insulation between the leads and the grounded tank. During operation, bushings continuously carry load currents and withstand short-circuit currents during external faults, ensuring stable power transmission and grid reliability. Failure to address bushing faults promptly can lead to severe consequences, jeopardizing the entire power system.
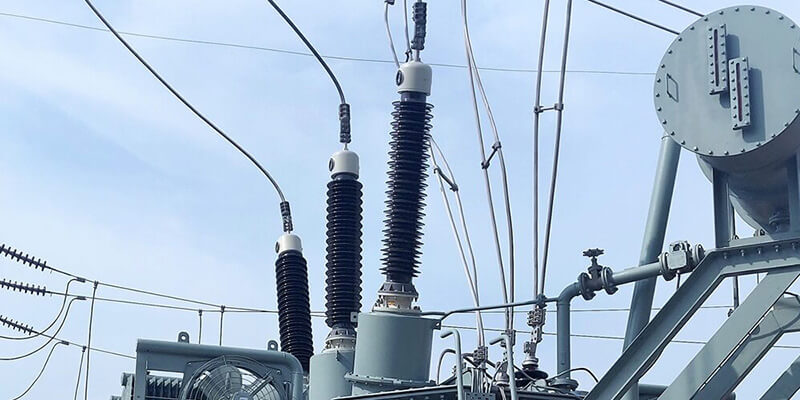
Causes of Bushing Failures
1.Manufacturing Defects
- Poor sealing at terminals, leading to moisture ingress, internal partial discharges, and eventual flashover or explosion.
- Capacitive core defects (e.g., misaligned screens, improper aluminum foil sizing, folded insulation layers, or residual air bubbles) causing electric field distortion, partial discharges, or breakdown.
- Improper grounding of the end screen, loose welding of leads, or electromagnetic vibration-induced grounding failures.
- High electric stress on capacitive screens, accelerating insulation aging and leading to breakdown.
2.Operational & Maintenance Errors
- Inadequate vacuum oil filling, oil leaks, or moisture ingress degrading insulation.
- Bent lower voltage grading spheres contacting conductive tubes, creating parasitic currents and localized overheating.
- Improper disassembly during testing, causing contact overheating or broken end-screen leads.
- Oil sampling errors (e.g., insufficient refilling or loose plugs) leading to leaks.
- Overvoltage from lightning strikes, switching surges, or surface contamination-induced flashovers.
3.Design & Assembly Flaws
Mismatched thread tolerances between conductive tubes and winding leads, increasing contact resistance and overheating.
Use of low-temperature solder (e.g., tin) for lead connections, risking meltdown at 200°C.
Common Bushing Faults
1.Overheating
Caused by poor internal/external contact or excessive load.
2.Oil Leakage
Aging seals or uneven flange connections at the base.
3.High Acetylene in Insulation Oil & End-Screen Discharge
Design flaws or ungrounded end screens.
Fault Handling Measures
1.Overheating Fault Resolution
Welding Quality:
- Polish surfaces thoroughly before welding.
- Apply uniform heat and use phosphor copper solder to fill gaps, ensuring sufficient contact area.
Crimping Quality:
- Match lead and connector diameters.
- Ensure adequate crimp length and use standardized crimping methods.
2.Oil Leakage Resolution
- Use compatible nuts, clamps, and gaskets. For oversized cables, employ crimped terminals.
- Secure connections with dual nuts to enhance tightness and heat dissipation.
- Avoid prolonged overloading through proper load distribution.
- Conduct regular inspections and address leaks immediately.
3. Acetylene & End-Screen Discharge Resolution
- Replace faulty bushings with certified units after rigorous testing.