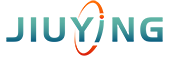
What Are You Looking For?
The core assembly of a three-phase oil-immersed transformer comprises a sealed magnetic circuit system consisting of laminated silicon steel cores and windings. The complete structure includes the following key components:
(1) Iron Core Assembly
As the magnetic flux pathway, the iron core minimizes energy losses through the use of 0.35-0.5mm-thick silicon steel laminations coated with insulating oxide films. The vertical section (core column) supports both high and low voltage windings, while the horizontal yoke forms a closed magnetic loop. This configuration optimizes magnetic flux distribution and reduces core losses.
(2) Transformer Winding
The electrical circuit consists of primary and secondary windings:
(3) Tank Assembly
The welded steel tank serves multiple functions:
Transformer oil specifications:
(4) Conservator System
The expandable oil reservoir (10% tank volume) features:
(5) Bushing System
Insulating assemblies connect internal windings to external circuits:
(6) Explosion-proof Device
Safety valve system:
(7) Gas Relay Protection
Differential protection system:
(8) Temperature Monitoring
Critical parameters:
(9) Neutral Point Grounding
System protection requirements:
(10) On-load Tap Changer
Voltage regulation system:
(1) Normal Operating Modes
A. Rated Conditions
B. Permissible Overloads
(2) Abnormal Conditions & Responses
A. Immediate Shutdown Criteria
B. Overload Management Protocol
C. Gas Relay Activation Procedure
(3) Maintenance Requirements
A. Routine Inspection Items
B. Periodic Maintenance Schedule
C. Specialized Testing
This technical specification provides comprehensive guidelines for the operation, maintenance, and troubleshooting of three-phase oil-immersed transformers, emphasizing safety compliance and equipment longevity through systematic condition monitoring.