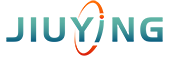
What Are You Looking For?
High-voltage transformer bushings are critical components in power transformers, facilitating the safe passage of conductors through grounded barriers while providing necessary insulation. This study examines a unique overheating defect in a 500kV oil-impregnated paper (OIP) transformer bushing, attributed to internal circulating currents induced by structural design flaws. The analysis encompasses diagnostic tests, disassembly inspections, and structural evaluations to elucidate the defect's root causes and propose effective remediation strategies.
In high-voltage power systems, transformer bushings serve as essential interfaces between internal transformer components and external circuits. They must withstand electrical, thermal, and mechanical stresses, as well as environmental factors such as humidity and temperature fluctuations. Failures in transformer bushings can lead to transformer outages or catastrophic events like explosions and fires. Despite their importance, effective monitoring and maintenance of transformer bushings remain challenging. Traditional diagnostic methods, including infrared thermography and periodic electrical testing, often fail to detect localized defects. This study investigates an atypical overheating defect in a 500kV transformer bushing, providing insights into its diagnosis and prevention.
The defective transformer bushing, model BRLW1-550/1250-3, was manufactured in 2002 and installed in a 500kV substation. In November 2021, during pre-commissioning tests for a new installation, oil chromatographic analysis revealed elevated total hydrocarbon levels in phases B and C, exceeding the attention threshold of 150 μL/L. The presence of gases such as H₂, CH₄, and C₂H₆, with a C₂H₆/C₂H₄ ratio greater than 1, indicated low-temperature thermal faults below 150°C. Additionally, dielectric loss measurements showed significant discrepancies among the phases, with phase C exhibiting the highest values, correlating with the chromatographic findings. Black suspended particles were also observed in the oil of phase C, further signaling internal degradation within the transformer bushing.
3.1 Pre-Disassembly Diagnostics
To further investigate the overheating issue in the transformer bushing, the affected units were returned to the manufacturer for comprehensive testing. Standard electrical tests, including insulation resistance, capacitance, and dielectric loss, confirmed the initial findings. Frequency Domain Spectroscopy (FDS) tests revealed that phase C had a higher dielectric loss at low frequencies, suggesting moisture ingress or insulation degradation. These results warranted a detailed disassembly for internal inspection.
3.2 Disassembly Findings
Upon disassembly of phase C, several anomalies were noted:
The insulating oil contained substantial black suspended matter, which was soft to the touch.
The capacitor core surface was coated with black deposits, while inner layers remained clean.
Corrosion or burn marks were present on the positioning sleeve's surface, accompanied by black viscous substances.
Similar, albeit less severe, signs were observed in phase B, while phase A appeared unaffected. These findings pointed to localized overheating and degradation inside the transformer bushing.
4.1 Induced Circulating Current Calculation
The transformer bushing's design includes a positioning sleeve between the wound tube and the assembly tube, with a 0.5mm assembly gap. This configuration creates a cantilever structure susceptible to vibrations during operation. These vibrations can cause intermittent contact between the tubes, forming a closed loop that allows circulating currents. Analytical calculations and finite element simulations estimated an induced electromotive force of approximately 17.9 mV and a circulating current of about 31 A under nominal operating conditions—sufficient to trigger localized overheating within the transformer bushing.
4.2 Electrochemical Corrosion at Copper-Aluminum Interface
The circulating currents generate localized heating at the contact points, leading to thermal degradation of the insulating oil and the formation of conductive carbonaceous deposits inside the transformer bushing. Scanning electron microscopy identified these deposits as primarily carbon and oxygen. X-ray photoelectron spectroscopy further revealed the presence of copper and copper oxide on the aluminum sleeve surface, indicating galvanic corrosion. The presence of corrosive sulfur compounds in the oil exacerbates this effect, facilitating the electrochemical reactions that degrade the interface.
The root cause of the defect lies in the inadequate mechanical fixation between the wound tube and the assembly tube within the transformer bushing, allowing for movement and intermittent contact. To mitigate this, the design was modified to include insulated positioning at both ends of the tubes, with a single-point equipotential connection. This approach ensures mechanical stability while preventing the formation of circulating current loops. After implementing these changes, the transformer bushings were reassembled and tested, showing no further anomalies in oil chromatographic analyses.
This case study highlights a unique overheating defect in a 500kV high-voltage transformer bushing, resulting from structural design flaws that permitted internal circulating currents. The ensuing localized heating led to oil degradation, formation of conductive deposits, and electrochemical corrosion at the copper-aluminum interface. Through comprehensive diagnostics and structural modifications, the defect was effectively addressed. This analysis underscores the importance of meticulous mechanical design in high-voltage transformer bushings to prevent such failures and ensure reliable operation.