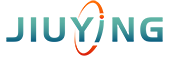
What Are You Looking For?
Transformers utilize electromagnetic induction to transfer electrical energy between circuits without direct contact, enabling voltage step-up or step-down to supply appropriate power for equipment with different voltage requirements. Windings, the fundamental components of transformers, serve as the magnetic field-generating and energy-transferring pathways. Typically made of insulated aluminum or copper wire, windings are categorized as primary (input) and secondary (output) coils. Based on voltage levels, they are termed high-voltage (HV) or low-voltage (LV) windings. Most transformers adopt concentric winding arrangements, with HV and LV coils wound into cylindrical layers around the iron core, separated by insulation. Generally, LV windings are placed inward while HV windings are positioned outward. This design prioritizes two key factors:
1.Insulation Considerations
Since the transformer core is grounded, placing LV windings closer to the core simplifies insulation. If HV windings were adjacent to the core, their high voltage would demand excessive insulation materials and spacing, increasing size and material costs.
2.Structural and Process Optimization
Voltage regulation in transformers is achieved by adjusting winding taps (i.e., altering turns). HV windings, handling smaller currents, typically incorporate taps. Positioning HV windings externally facilitates tap connection, improves soldering quality, enhances heat dissipation for tap switches, and addresses current balancing in on-load tap changers.
Note: Transformer designs vary based on application. While most place HV windings externally, exceptions exist—e.g., HV windings may be internal in specialized cases (e.g., low-voltage/high-current scenarios like furnace or welding transformers). Some adopt interlaced winding layouts (alternating HV/LV layers) to improve mechanical strength, reduce leakage reactance, and simplify terminal connections, despite increased insulation complexity.