The installation of power transformers is a complex and critical task that must adhere to technical standards to ensure the safety and stability of transformer operation. Below are the key considerations during the installation process of power transformers:
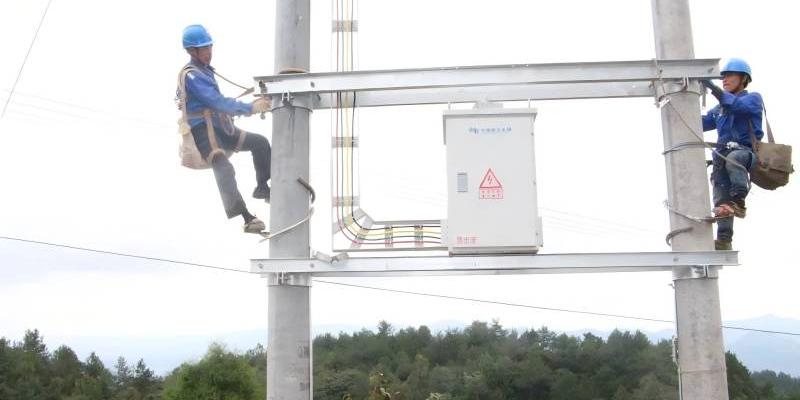
1. Transporting the Transformer
During transport, transformers are typically handled using lifting equipment. Specific precautions include:
- Lifting considerations: Use the lifting lugs on the transformer oil tank walls and avoid using the lifting rings on the tank cover. The hook should align with the center of the transformer, and the angle between the lifting sling and the vertical line should not exceed 30°. If necessary, use a dedicated lifting beam.
- Securing during transport: Ensure the transformer is stable during transport. When placed on a trailer, the base should be supported by wooden blocks and secured with ropes to prevent slipping or tipping during transport. The speed should be limited to 1–15 km/h, especially when going uphill, downhill, or making turns, to prevent shock and vibration damage.
- Short-distance transport: The transformer can be moved using its base rollers on a track, with a maximum speed of 0.2 km/h. The pulling force should be applied below the center of gravity.
2. Internal Inspection of the Transformer
After arriving at the installation site, a thorough inspection of the transformer’s internal components is required to ensure no damage or loosening occurred during transportation. The following conditions allow for skipping the internal inspection:
- The manufacturer’s instructions state that internal inspection is unnecessary.
- Transformers with a capacity of 100 kVA or less that have been transported without incident.
- Short-distance transported transformers that were adequately supervised and free of shocks or severe vibrations.
3. Drying the Transformer
Whether a new transformer requires drying depends on several factors. Drying is generally not required if the following conditions are met:
- Oil-filled transport: The insulating oil’s electrical strength and moisture content tests are passed, and the insulation resistance and absorption ratio meet the requirements.
- Nitrogen-filled transport: The internal pressure remains positive from the factory to installation, and after adding qualified insulating oil, the oil's electrical strength and moisture content meet the requirements.
If drying is necessary, select an appropriate method based on the transformer's insulation condition, size, and structure, such as core loss drying, copper loss drying, vacuum hot oil spray, or infrared drying.
4. Oil Treatment
Transformers requiring drying often have insulation issues, so while drying the core, the insulating oil must also be treated to improve insulation performance and ensure normal operation.
5. Positioning the Transformer
Once the transformer passes inspection, it can be installed. For medium and small transformers that are transported fully assembled or with minimal disassembly, installation is relatively simple. Key points include:
- Aligning high and low voltage sides: When moving the transformer indoors, ensure the high and low voltage sides align with the corresponding equipment to avoid needing to reposition it later.
- Leveling the foundation rails: Ensure the transformer’s foundation rails are level and match the wheelbase of the transformer. For transformers equipped with gas relays, the top cover should have a 1%–1.5% slope towards the gas relay to allow gases generated from internal faults to enter the relay.
- Fixing rollers: Once positioned, transformers with rollers should have them secured with removable braking devices.
- Connecting the busbar: When connecting high and low voltage busbars to the bushings, use two wrenches to avoid twisting the bushing bolts and ensure a tight connection.
- Grounding: Ground the transformer’s low-voltage neutral terminal and connect the foundation rails to the grounding conductor. The grounding wire should be copper or steel, and the joints should be securely connected to prevent corrosion.
6. Transformer Testing
After installation, transformers undergo a series of tests to ensure compliance with standards and operational requirements. Typical tests include:
- Measuring winding and bushing resistance.
- Verifying the tap ratio of all taps.
- Checking the connection group of three-phase transformers and the polarity of single-phase transformer terminals.
- Measuring insulation resistance, absorption ratio, or polarization index for the windings and bushings.
- Conducting a 1-minute AC voltage withstand test on the windings and bushings.
- Testing transformer oil for electrical strength and moisture content.
7. Trial Operation of the Transformer
Trial operation involves energizing the transformer and operating it under load for 24 hours. This is the final quality test for the transformer. Before trial operation, conduct a full inspection, including topping off oil and checking for leaks. The transformer typically undergoes five no-load full-voltage energizations, followed by a 24-hour no-load operation. If no issues are detected, the transformer is placed under load for an additional 24 hours. If everything remains normal, the trial operation is considered successful.
Summary
The installation of power transformers must be carried out strictly in accordance with standards, from transportation, inspection, and drying to oil treatment, positioning, testing, and trial operation, to ensure safe and stable operation.