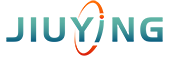
What Are You Looking For?
How can you replace the insulating liquid in an old mineral oil transformer with natural ester?
Here are 10 key points to follow:
Conduct routine tests on the transformer to evaluate the aging status of its insulation system. Sample and analyze the oil to determine the necessity and feasibility of replacement.
Material compatibility is critical for the long-term stable operation of the transformer. Confirm with the ester oil manufacturer whether all materials in contact with the insulating oil are compatible. If needed, perform compatibility tests, oil mixing tests, and performance evaluations. For incompatible materials, provide replacement solutions.
Follow safety protocols and take necessary precautions. Ensure all equipment is properly grounded and refer to the transformer's manual for specific instructions.
Drain the transformer through the oil drain valve, aiming to remove as much residual oil as possible. Minimize residual old oil to avoid contamination.
Aged gaskets in old transformers may cause oil leaks. Replace them with materials compatible with natural esters, such as hydrogenated nitrile rubber (HNBR), silicone rubber, or fluororubber.
Flush the transformer with natural ester heated to 50–70°C to clean residual oil from valves, pipelines, and radiators. This process also removes sediment from the bottom of the transformer. Control the flushing pressure to avoid damaging components.
Use a filter with a pore size no larger than 1μm. Maintain the oil temperature at 50–70°C to expedite the process. If necessary, use vacuum filling for better results.
Clean up any spilled oil on the transformer's exterior and attach natural ester labels. Allow the transformer to settle for 8–24 hours to eliminate air bubbles. Ensure proper dust protection during this period.
Collect oil samples for testing to confirm quality and ensure no leaks. Record all relevant data promptly.
Perform acceptance tests as per standards, check gaskets for leaks, and put the transformer into service. Conduct regular oil sampling for ongoing performance monitoring.
1.When electrical equipment requires additional oil, prioritize unused insulating oil that meets relevant standards.
2.Use the same base oil, brand, and additive type whenever possible. Ensure the added oil meets or exceeds the existing oil's specifications.
3.Avoid mixing natural esters with different base oils unless absolutely necessary. If mixing is required, conduct compatibility tests.
4.In compatibility tests, use the actual mixing ratio or default to a 1:1 ratio if unknown.
5.If the amount of new oil added is minimal (e.g., less than 5%), the risks are typically lower.