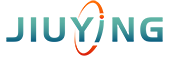
What Are You Looking For?
The windings and core of a transformer are the primary components responsible for transferring and converting electromagnetic energy. Ensuring their reliable operation is a key concern. Statistics show that core-related faults rank third among all transformer faults. Manufacturers have focused on addressing core defects and have introduced technical improvements such as grounding monitoring for metal flexible hoses and stainless-steel hoses of the core and ensuring single-point grounding.
Operational departments have also prioritized detecting and identifying core faults. However, transformer core faults, primarily due to multi-point grounding and poor grounding, continue to occur frequently. This article introduces methods for identifying and addressing these two fault conditions.
During normal transformer operation, an electric field exists between the energized windings and the oil tank. The core and other metallic components are immersed in this field. Uneven capacitance distribution and varying field strength mean that if the core’s metal flexible or stainless-steel hoses are not grounded, charging and discharging may occur. This can compromise the insulation of solid materials and oil, necessitating a single-point grounding for the core.
The core, made of silicon steel sheets and metallic hoses, is insulated between layers to reduce eddy currents, typically with resistances of a few ohms to several tens of ohms. Due to the significant capacitance between layers, these layers act as pathways in an alternating electric field. A single-point grounding suffices to clamp the potential of the entire core stack to the ground potential.
However, if the core or its metal components have two or more grounding points, closed loops may form between these points. These loops can link magnetic flux, induce electromotive force, form circulating currents, cause localized overheating, and even burn the core. Therefore, single-point grounding of the transformer core is essential.
Core faults primarily stem from two causes:
1.Poor construction leading to short circuits.
2.Multi-point grounding caused by accessories, metal hoses, and external factors.
1.Failure to remove or reverse the positioning pins transported with the oil tank lid after transformer installation can create multiple grounding points.
2.Core laminations bending upwards to touch clamping structures, or clamping plates being too close to the core columns, causing grounding.
3.Excessively long bushings on yoke bolts, leading to contact with the yoke laminations and creating new grounding points.
4.Insulation paperboards between the core clamp and yoke becoming dislodged or damaged, allowing contact.
5.In large and medium transformers with submersible pumps, metal debris from worn pump bearings can accumulate at the oil tank bottom and form conductive bridges under electromagnetic force.
6.Thermometer sleeves on the oil tank cover being too long and touching clamping structures or yoke edges, causing grounding.
7.Metallic foreign objects falling into oil-immersed transformers and bridging the core laminations and tank body.
8.Contaminated or damp wooden blocks between the clamp and yoke reduce insulation resistance, resulting in zero resistance and multi-point grounding.
1.Eddy currents in the core increase iron loss and cause localized overheating.
2.Prolonged multi-point grounding can overheat the transformer, leading to oil and winding insulation degradation. This may cause the insulation between core laminations to deteriorate, exacerbating overheating and potentially destroying the core.
3.Multi-point grounding over time can degrade transformer oil, producing combustible gases that trigger gas relay actions.
4.Overheated cores can carbonize wooden spacers and clamps inside the transformer.
5.Severe multi-point grounding may sever the grounding wire, leaving the transformer without proper grounding, with disastrous consequences.
6.Multi-point grounding may also cause discharge phenomena.
Detection methods include:
1.Gas Chromatography Analysis
If the levels of methane and olefins in the gas analysis are high while carbon monoxide and dioxide levels remain stable, it indicates core overheating, possibly due to multi-point grounding. Acetylene presence suggests intermittent multi-point grounding.
2.Measuring Grounding Wire Current
Use a clamp meter to measure current in the core grounding wire. Normally, the grounding current is minimal (below 0.3A) since no current loop exists. Multi-point grounding creates short-circuited loops with circulating currents depending on the relative position of fault and grounding points. Current may reach tens of amperes, making this a precise method for diagnosing multi-point grounding faults.
1.Disconnecting Grounding Wire
If the fault current is significant, temporarily disconnect the grounding wire. Continuous monitoring is necessary to prevent floating potential after fault resolution.
2.Inserting a Variable Resistor
For unstable faults, insert a variable resistor in the grounding wire to limit current below 1A. The resistor value is determined by dividing the measured voltage by current.
3.Fault Point Relocation
Relocate the core’s grounding to the fault point to significantly reduce circulating current.
4.Chromatographic Monitoring
Monitor gas generation rates at the fault point using chromatographic analysis.
For transformers that can be shut down, the multi-point grounding fault must be eliminated by:
Direct Current Method
Disconnect the core and clamp connections. Apply 6V DC to the yoke laminations and measure voltage between laminations. A zero or reverse voltage indicates a fault point.
Alternating Current Method
Supply 220–380V AC to the transformer’s low-voltage windings. Measure current with a milliampere meter. Zero current indicates a fault point.