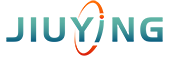
What Are You Looking For?
Whether it is an oil-immersed transformer or a dry-type transformer, during operation, due to the presence of core losses and copper losses, these losses will convert into heat energy and dissipate outward, causing the transformer to continuously heat up and increase in temperature. Specifically, the heat generated by the core and copper losses will gradually raise the temperature of the core and windings. Initially, the temperature rises rapidly, but as the temperature of the core and windings increases, they will develop a temperature difference (also called temperature rise or temperature differential) with the surrounding cooling medium (such as oil or air). At this point, the windings and core will transfer part of the heat to the surrounding medium, causing the temperature of the medium to rise. As heat is transferred from the windings and core to the surrounding medium, the rate of temperature rise of the windings and core will slow down. After a period of time, the temperature of the windings and core will eventually stabilize and will no longer increase. At this point, the heat generated by the windings and core will be entirely dissipated into the surrounding medium. This is called the thermal equilibrium state. This process is governed by the laws of "heat transfer."
In the thermal steady state (thermal equilibrium), the path of the heat flow is complex. In oil-immersed transformers, the following characteristics generally exist:
1.Heat Transfer from Windings and Core: The heat generated by the losses in the windings and core will first be transferred from the hottest internal points of the windings and core to the surface that contacts the oil through conduction. Therefore, the surface temperature is always lower than the temperature of the hottest internal point. Figure 6-1 shows the temperature distribution in the radial direction inside the windings.
When conducting temperature rise tests and calculations for the windings, only the average temperature rise of the windings can be obtained. The temperature of the hottest point in the windings is usually 10-15°C higher than the average temperature rise. As mentioned earlier, the temperature rise at the hottest point is crucial in determining the transformer's load capacity. Although methods like fiber optic temperature measurement can be used to measure the temperature at the hottest point of the windings, such equipment is expensive and has not been widely adopted.
2.Heat Transfer to Oil: After the heat from the windings and core is transferred to the surface, the surface temperature of the windings and core will be higher than the temperature of the surrounding oil, transferring heat to the oil in contact with the windings and core, gradually increasing the oil temperature.
Generally, the average temperature of the windings is 20-30°C higher than the average oil temperature (this means the temperature rise of the windings relative to the oil is typically 20-30°C). In design, it is commonly controlled by experience to keep the temperature rise of the windings relative to the oil below 25K.
3.Convection of Oil: Once the oil near the windings and core is heated, it will naturally flow upward, while the cooled oil flows downward. This is the convection of the oil (since oil has poor heat conduction properties, it relies mainly on convection), which leads to a general increase in the temperature of the oil inside the transformer tank. Furthermore, because hot oil flows upward and cold oil flows downward, the oil at the top of the tank is always hotter than at the bottom. Typically, the temperature of the upper oil layer is about 20% higher than the average oil temperature.
Figure 1 illustrates the flow direction of the oil in the winding's oil passages, Figure 2 shows the convection direction of oil in a tubular tank and the axial temperature rise distribution, and Figure 3 shows the radial temperature rise distribution.
4.Heat Transfer from Oil to the Surroundings: The heated oil near the windings and core, due to convection, moves within the oil tank. When hot oil encounters the tank wall or cooling pipes, part of the heat is transferred to the wall or pipe, causing the oil temperature to decrease and become cooler oil that flows downward. Additionally, the tank wall or pipe wall, after absorbing heat, increases in temperature. The tank or pipe wall also creates a temperature difference with the surrounding medium (air). Once the heat has been transferred to the outer surface, it will be dissipated into the air by convection and radiation.
In summary, the heat generated by the windings and core of the transformer is transferred to the outside air through many parts of the transformer. Each part of the heat flow path generates a temperature difference, and the size of this temperature difference depends on the loss values and the physical properties of the medium. The temperature rise calculation of the transformer involves calculating the temperature differences in various parts, including the temperature difference between the windings and oil, the core and oil, the windings and air, the core and air, the oil and air, and the difference between the maximum oil temperature at the top layer and the surrounding air temperature.
The analysis above mainly concerns the heating and cooling process of oil-immersed transformers. For dry-type transformers, the heating and cooling process is simpler. Generally, the heat from the core and windings of dry transformers is first transferred to the surrounding solid insulating medium (such as epoxy resin) and then transferred to the air through the surface of the medium by convection and radiation.